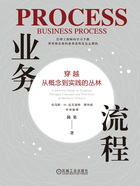
推荐序二
I am excited to see this book on process management from George Chen for several reasons. Primary among them is that the book suggests a rebirth of thinking about how a process orientation benefits businesses. A generation ago, process management and process reengineering were very popular in large organizations around the world. And no wonder: process redesign and the management of large, end-to-end processes were unmatched at aligning work in the direction of customers and coordinating work across departments. Process reengineering encouraged companies to re-imagine how these processes work, bringing the information technologies of the time to bear. Reengineering enjoyed many successes, although in the US it sometimes devolved into mindless job cuts.
Perhaps for that reason, it fell out of fashion in many companies. In addition, process thinking required a “left-to-right” focus, in the direction of customers, putting it at odds with more traditional functional and hierarchical “top-down” management. Employees wondered, “who do I report to, the process manager or my line manager?” For many companies the benefits were not worth the effort required to resolve the management conflicts.
As George Chen describes in this book, however, a process isn't complicated. It's simply a sequence of tasks to create a specified outcome. Its value is in understanding how the sequence of tasks fit together and making improvements. It applies at multiple levels——from work performed by individuals or a small work group, key activities within a department, and to end-to-end processes that cut across the organization.
Process management has a long history, some of which is detailed in this book. It includes Frederick Taylor's work in measuring and improving physical labor tasks, Walter Shewhart's introduction of statistical quality control, W. Edwards Demings' efforts to improve quality processes and their extension into “Total Quality Management”, the radical change-focused business process reengineering movement of the 1990s, and most recently, the Six Sigma and Lean approaches to incremental process improvement. I am a proponent of all types of process improvement and management, although business process reengineering is the only one that addresses broad, end-to-end processes. Some liken digital transformation to process reengineering, but most of these transformation programs have lacked a structured, measured approach to improving and managing operations.
Although there are important differences among these approaches, the fact that the notion of process keeps reappearing in business is testimony to its importance. There is a permanent need in organizations to improve operational performance, and managing processes is a reliable way to do so. Process thinking may have been somewhat less popular over the past couple of decades, but today I believe that a “new process calculus”is emerging and that it is time for senior leaders to put process management back on their radar screens. Much of that calculus ultimately stems from technology: both technologies that reduce the tedium of process management (such as process mining) and potentially game-changing technologies such as AI that are easier to implement when processes are well-defined and managed.
The availability of these new technologies is a key reason that companies should return to large-scale process management today. A lack of technology support——particularly in incremental process improvement approaches like Lean and Six Sigma——contributed to the decline in popularity of process thinking. Specifically, several new technologies have made business processes either easier or more beneficial to manage. They include process mining and process intelligence, process design tools, business process management systems, and AI for process improvement and enablement. This book is one of the first to consider how these new tools can benefit process management in organizations.
Process management can also improve productivity. Key to productivity gains is to measure and improve business processes, employ intermediate metrics in cycle time and error rates, and ultimate measures in money saved or earned. And because of new technologies, measurement of process performance is increasingly becoming automated. Better managing and improving processes increases productivity by reducing error rates, cycle times, and work that doesn't contribute to desired process outcomes. And new technologies help increase scale, further boosting productivity.
George Chen's book suggests that the motivations for companies to employ process management are higher and the difficulties of doing so are lower than ever before. On the motivation side, there is a virtuous cycle among productivity gains, easier implementation of technology, and better data; on the difficulties side there are numerous technologies that make the work more palatable. Those organizations that have consistently applied process thinking to their operations have reaped the benefits.
It is not just in China that process management is succeeding. In Europe, companies like Siemens, BMW, and Reckitt have had process management in place for many years. Siemens, despite having a highly decentralized set of business units, has pursued common processes and much more digitized and efficient process designs in areas like order management and purchase-to-pay. BMW has standardized most of its global production processes, which used to vary greatly around the world, and is now focused on support process optimization. The consumer products company Reckitt has combined the organizations for process excellence, process mining, and process automation under an overall banner of digital transformation.
In North America, a number of companies have discovered or rediscovered process management, but are somewhat less likely to be addressing a broad range of processes. Instead they are often focusing on a particular process domain in order to achieve savings and time reductions. Uber (customer service processes), Pepsico (accounts receivable and payable processes), Cardinal Health (order management), Johnson & Johnson (supply chain) and GE Healthcare (financial processes) are examples of organizations that have made significant improvements across major processes.
In short, process can be the unifying link among people, technology, data, analytics, and AI——and marshal them to improve business performance. It can orchestrate a marriage of sorts among these different resources. Process needs to lie at the core because it is how organizations deliver value to customers. Like most good marriages, there will be plenty of challenges to work through. So, it is time for senior managers to put“process”back on their radar screens and to begin to sort out how to make it work in their companies.
After reading this book carefully, organizations that are serious about transforming their operations with AI or who need to dramatically improve their cost or quality positions should strongly consider a major process effort. Process management is the right answer for companies and government organizations that believe that the efficiency and effectiveness of their operations, and how they deliver high-quality outcomes to customers, are critical to their success. It's also very helpful for organizations who wish to get substantial economic value from their technology investments. Of course, each of these things should be true of every company. I hope that the book is widely read across China and the world.
Thomas H. Davenport
Distinguished Professor, Babson College and Fellow, MIT Initiative on the Digital Economy Author of Process Innovation, Competing on Analytics, and All In on AI
我很高兴看到陈果写的这本关于流程管理的书,原因有几个,其中最主要的一点是,这本书重新提出了流程导向如何使企业受益的思考。流程管理和流程再造曾在世界各地的大型组织中非常流行。毫无疑问,流程重设计和对大规模、端到端流程的管理,在以客户为中心来对齐工作以及跨部门协调工作方面是无与伦比的。流程再造则鼓励公司利用当时的信息技术重新设想流程是如何运作的。流程再造取得了许多成就,尽管在美国,它有时会演变成盲目的裁员。
也许正是因为这个原因,流程再造在许多公司已经不再流行了。此外,流程思维需要以客户为导向、横向贯通的关注,这与传统的职能上和层级上“自上而下”的管理模式相矛盾。员工们想知道:“我向谁汇报工作,是流程经理还是直线经理?”对许多公司来说,解决管理冲突所需付出的努力并不值得其所带来的收益。
然而,正如陈果在这本书中所描述的,一个流程并不复杂。它只是创造特定成果的一个任务序列。流程管理的价值在于理解任务序列如何组合在一起,为企业带来改进。它适用于多个层级——从个人或小型工作组执行的工作、部门内的关键活动,到跨组织的端到端流程。
流程管理有着悠久的历史,该书有一些详细介绍,包括弗雷德里克·泰勒在测量和改进体力劳动任务方面的工作,沃特·阿曼德·休哈特对统计质量控制的采用,威廉·爱德华·戴明改善质量流程的努力及以此为基础的“全面质量管理”的诞生,20世纪90年代激进的以变革为中心的业务流程再造运动,以及最近的为了持续改进流程的六西格玛和精益管理方法。我是所有类型的流程改进和管理的支持者,尽管“业务流程再造”是目前唯一一种处理广泛的端到端流程的方法。有些人将数字化转型比作流程再造,但大多数转型项目缺乏结构化的、可衡量的方法来改进和管理运营。
尽管这些方法之间存在重要的差异,但流程的概念在企业中不断出现的事实证明了它的重要性。在组织中,提升运营绩效是一种永久的需求,而管理流程则是满足这种需求的可靠方法。在过去的几十年里,流程思维的普及度可能有所下降,但是今天我相信一种“新的流程演算”正在出现,高层领导者是时候再次重视起流程管理的作用了。这种演算在很大程度上最终源于技术,既有可以减少流程管理枯燥乏味的技术(如流程挖掘),也有可能改变游戏规则的技术(如人工智能),当流程被明确定义和良好管理时,这些技术更容易实施。
这些新技术的可用性是当今企业应该回归大规模流程管理的关键原因。缺乏技术支持(特别是在像精益管理方法和六西格玛这些增量流程改进方法中)导致流程思维的普及度下降。具体来说,一些新技术使业务流程更容易管理或能产生更多收益。它们包括流程挖掘和流程智能、流程设计工具、业务流程管理系统,以及用于流程改进和流程实现的人工智能。这本书正是率先考虑这些新技术如何使组织的流程管理受益的代表作。
流程管理还可以提高生产力。提高生产力的关键在于衡量和改进业务流程,并且在处理时间和错误率方面应用过程性指标,在成本节降或利润提升方面应用结果性指标。由于新技术的出现,流程绩效的衡量越来越自动化。可以通过降低错误率、缩短处理时间以及削减不能产生预期流程结果的工作来更好地管理和改进流程,从而提高生产力。新技术有助于扩大规模,进一步提高生产力。
陈果的书表明,当前企业采用流程管理的动机比以往任何时候都要强烈,而这样做的难度比以往任何时候都要低。在动机方面,生产力的提高、更容易的技术实施和更好的数据之间存在一个良性循环;在困难度方面,有许多技术使工作更容易开展。那些始终如一地将流程思维应用于其运营的组织已经从中获益。
流程管理不只在中国正在取得成功,在欧洲,西门子、宝马和利洁时等公司已经实施流程管理多年。尽管西门子的业务单元高度分散,但它在诸如订单管理、采购到付款等领域一直追求通用流程以及更加数字化和高效的流程设计。宝马已经将它在全球的大部分生产流程标准化,这些流程过去在世界各地的差异很大,宝马现在专注于支持性流程的优化。消费品公司利洁时在数字化转型的大旗下,将流程卓越、流程挖掘和流程自动化的组织整合起来。
在北美,许多公司已经发现或重新发现了流程管理,但它们不太可能处理广泛的流程,相反,它们通常专注于特定的流程域,以实现成本节降和效率提升。优步(客户服务流程)、百事可乐(应收账款和应付账款流程)、卡地纳健康(订单管理)、强生(供应链)和通用电气医疗(财务流程)都是在主要流程上取得重大改进的案例。
简言之,流程可以是人员、技术、数据、分析和人工智能间的纽带,可以将它们组织起来以提高业务绩效。它可以协调这些资源之间的各种“联姻”。流程需要处于核心位置,因为它是组织向客户交付价值的方式。就像大多数美满的婚姻一样,这里的“婚姻”也会有许多挑战需要克服。因此,高级经理们是时候再次重视起“流程”,并思考如何让它在企业中发挥作用了。
在仔细阅读了这本书之后,那些认真考虑用人工智能来改变它们的运营,或者需要显著改善其成本或质量状况的组织,应该着重考虑流程管理努力的重点。对那些相信运营的效率和有效性以及向客户交付高质量成果对其成功至关重要的公司和政府机构来说,流程管理是正确的答案。对希望从技术投资中获得巨大经济价值的组织来说,它也非常有帮助。当然,这应该适用于每一家公司。我希望这本书在中国乃至世界各地被广泛阅读。
托马斯·H.达文波特
巴布森学院杰出教授、麻省理工学院数字经济倡议研究员、《流程创新》《基于大数据分析的竞争》《全情投入人工智能》等书的作者