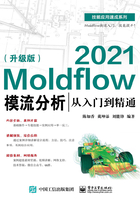
1.3 塑件缺陷产生的原因及对策
在塑件成型加工过程中,由于塑料原料品种繁多,模具型腔结构复杂,成型设备的控制运行状态各异,加上成型工艺的差异等,在塑件上会产生各种各样的成型缺陷。
1.3.1 欠注
1.表现
型腔未完全充满,主要发生在远离浇口或薄截面的地方,如图1-14所示。

图1-14 欠注
2.物理原因
熔料的注射压力太小和注射速度太低,熔料在射向流道最末端的过程中逐渐冷却。通常在低熔料温度和模温的条件下注射高黏性材料时会碰到这种情况。它也会发生在需要高压注射,但保压压力设置小、不成比例的时候。
实际上,当需要较大的注射压力时,保压压力也应按比例增大:正常时,保压压力应为注射压力的50%左右,但如果采用较大的注射压力,保压压力应为注射压力的70%~80%。
如在浇口附近发现注射不满,可以解释为流体前锋在这些点被阻挡,较厚的地方先被充满。因此,在型腔几乎被充满之后,在薄壁处的熔料已经凝结并且在流体中心部位有少量的流动会导致注射不足。
3.加工原因
与加工参数有关的原因与改良措施如表1-4所示。
表1-4 与加工参数有关的原因与改良措施

4.设计原因
与设计有关的原因与改良措施如表1-5所示。
表1-5 与设计有关的原因与改良措施

1.3.2 飞边
1.表现
在凹处周围,沿分型线的地方或模具密封面出现薄薄的飞边,如图1-15所示。

图1-15 飞边
2.物理原因
在多数情况下,飞边的产生是因为在注射和保压过程中,机器的合模力不够,无法沿分型线将模具锁紧并密封。
如果型腔内有的地方压力很大,此处模具变形就有可能造成溢模。在高的成型温度和注射速度条件下,熔料在流道末端仍能充分流动,如果模具没有锁紧就会产生飞边。
如果只在模具上某一点发现飞边,就说明模具本身有缺陷,此处模具未完全封住。局部产生飞边是由于模具有缺陷,而扩展到整个周围则是因为合模力不够。
为避免飞边,在增加合模力时应该慎重,因为合模力过量易损坏模具。建议正确的做法是应仔细确认飞边产生的真正原因。
特别是在使用多型腔模具之前,准备一些模具的分析资料,这样可以给所有的问题提供正确答案。
3.加工原因
与加工参数有关的原因与改良措施如表1-6所示。
表1-6 与加工参数有关的原因与改良措施

4.设计原因
与设计有关的原因与改良措施如表1-7所示。
表1-7 与设计有关的原因与改良措施

1.3.3 缩痕
1.表现
塑件表面材料堆积区域有缩痕,如图1-16所示。缩痕主要发生在塑件壁厚最大的地方或者壁厚改变的地方。

图1-16 缩痕
2.物理原因
当塑件冷却时,收缩(体积减小,收缩)发生,此时外层紧靠模壁的地方先冻结,在塑件中心形成内应力。如果应力太大,就会导致外层的塑料发生塑性变形,换句话说,外层会向里陷下去。如果在收缩发生和外壁变形还未稳定(因为还没有冷却)时,保压没有补充熔料到模件内,在模壁和已凝结的塑件外层之间就会形成沉降。
这些沉降通常看作收缩。如果塑件有厚截面,在脱模后也有可能产生这样的收缩。这是因为内部仍有热量,它会穿过外层并对外层产生加热作用。塑件内产生的拉伸应力会使热的外层向里沉降,在此过程中形成收缩。
3.加工原因
与加工参数有关的原因与改良措施如表1-8所示。
表1-8 与加工参数有关的原因与改良措施

4.设计原因
与设计有关的原因与改良措施如表1-9所示。
表1-9 与设计有关的原因与改良措施

1.3.4 熔接痕
1.表现
在充模方式里,熔接痕是指各流体前端相遇时的一条线。熔接痕形成示意图如图1-17所示。特别是模具有高抛光表面的地方,塑件上的熔接痕很像一条刮痕或一道槽,这在颜色深或透明的塑件上更明显。熔接痕的位置总是在料流方向上。

图1-17 熔接痕形成示意图
2.物理原因
熔接痕形成的地方为熔料的细流分叉并连接在一起的地方,最典型的是型芯周围的熔流或使用多浇口的塑件。在细流再次相遇的地方,表面会形成接合缝和料流线。
熔流周围的型芯越大或浇口间的流道越长,形成的熔接痕就越明显。细小的熔接痕不会影响塑件的强度。
然而,流程很长或温度和压力不足的地方,充模不满会造成显著的凹槽,其主要原因是流体前端未均匀熔合产生了弱光点。聚合物内加入颜料的地方可能会产生斑点,这是因为在取向上有明显的差异。浇口的数量和位置决定了熔接痕的数量和位置。流体前锋相遇时的角度越小,接合缝越明显。
大多数情况下,工艺调试不可能完全避免熔接痕或料流线。所能做的是降低其亮度,或将它们移到不显眼或完全看不到的地方。
3.加工原因
与加工参数有关的原因与改良措施如表1-10所示。
表1-10 与加工参数有关的原因与改良措施

4.设计原因
与设计有关的原因与改良措施如表1-11所示。
表1-11 与设计有关的原因与改良措施

1.3.5 翘曲
1.表现
塑件的形状在塑件脱模后或稍后一段时间内产生旋转或翘曲现象,如图1-18所示。典型表现为塑件平坦部分有起伏,直边向里或向外弯曲或翘曲。

图1-18 翘曲
2.物理原因
塑件因其特性,冻结的分子链在应力作用下发生内部移位。在脱模的时候,按不同的塑件形状,应力往往会造成不同程度的变形。内应力使塑件收缩不均,小颗粒移位,颗粒内冷却不平衡或颗粒内产生过量的压力。特别是用部分结晶材料制成的塑件,如PE、PP、POM比非晶体材料ABS、PMMA和PC更容易产生缩壁,更易发生翘曲。
3.加工原因
与加工参数有关的原因与改良措施如表1-12所示。
表1-12 与加工参数有关的原因与改良措施

4.设计原因
与设计有关的原因与改良措施如表1-13所示。
表1-13 与设计有关的原因与改良措施

1.3.6 颜色不均
1.表观
颜色不均是指塑件表面的颜色不一样,可在浇口附近和远处出现,偶尔也会在锐边的料流区出现。
2.物理原因
颜色不均是颜料分配不均造成的,尤其是通过母料、粉状或液态色料加色时。
在温度低于推荐的加工温度情况下,母料或色料不能完全均化。当成型温度过高或在料筒的残留时间太长时,也容易造成颜料或塑料的热降解,导致颜色不均。
当材料在正确温度下进行塑化或均化时,如果通过浇口横截面时注射太快,可能会产生摩擦热而造成颜料降解和颜色改变。
通常,在使用母料和色料时,应确保颜料及其溶解液与需要上色的树脂在化学、物理特性方面相容。
3.加工原因
与加工参数有关的原因与改良措施如表1-14所示。
表1-14 与加工参数有关的原因与改良措施

4.设计原因
与设计有关的原因与改良措施如表1-15所示。
表1-15 与设计有关的原因与改良措施

续表

1.3.7 气泡
1.表现
塑件表面和内部有许多气泡(主要在浇口附近、流道中途和远离浇口的地方),发生在塑件壁最厚的地方。气泡有着不同的尺寸和不同的形状,如图1-19所示。

图1-19 气泡
2.物理原因
气泡主要发生在必须在高温下加工的热敏感性材料上。如果所需的成型温度太高,通过分子分裂而导致材料分解,熔料就有发生热降解的危险,成型过程中就容易产生气泡。
成型周期长,或因为料筒内的熔料过热,成型过程中都可能产生气泡。
3.加工原因
与加工参数有关的原因与改良措施如表1-16所示。
表1-16 与加工参数有关的原因与改良措施

4.设计原因
与设计有关的原因与改良措施如表1-17所示。
表1-17 与设计有关的原因与改良措施

1.3.8 空隙
1.表现
塑件内部的空隙表现为圆形或拉长的气泡形式。只有透明的塑件才可从外面看出里面的空隙;不透明的塑件无法从外面测出。空隙往往发生在壁相对较厚的塑件内,并且是在最厚的地方。
2.物理原因
当塑件内有泡产生时,经常认为是气泡,是模具内的空气被流入型腔的熔料裹入而形成的。另一个解释是由于料筒内的水汽和气泡进入了塑件的内部。所以,这样的“泡”的产生有多方面的原因。
一开始,生产的塑件会形成一层坚硬的外皮,并且视模具冷却的程度往里或快或慢地发展。然而在厚壁区域,中心部分仍继续保持较长时间的黏性,外皮有足够的强度抵抗任何应力收缩。结果导致平面的熔料被往外拉长,在塑件内仍为塑性的中心部分形成空隙。
3.加工原因
与加工参数有关的原因与改良措施如表1-18所示。
表1-18 与加工参数有关的原因与改良措施

4.设计原因
与设计有关的原因与改良措施如表1-19所示。
表1-19 与设计有关的原因与改良措施

1.3.9 放射纹
1.表现
从浇口喷射出的一股灰暗色熔流在稍微接触模壁后马上被随后注入的熔料包住。此缺陷可能部分或完全隐藏在塑件内部。
2.物理原因
放射纹往往发生在熔料进入型腔的过程中,流体前端停止发展的地方。它经常发生在大型腔的模具内,熔流没有直接接触到模壁或没有遇到障碍。通过浇口后,有些热的熔料接触到相对较冷的型腔表面后冷却,在充模过程中不能同随后的熔料紧密结合在一起。
除去明显的表面缺陷,放射纹伴随不均匀性、熔料产生冻结拉伸、残余应力和冷应变而产生,并且这些因素都会影响产品质量。
在多数情况下不太可能只通过调节成型参数进行改进,只有改进浇口位置和几何尺寸才可以避免放射纹的产生。
3.加工原因
与加工参数有关的原因与改良措施如表1-20所示。
表1-20 与加工参数有关的原因与改良措施

4.设计原因
与设计有关的原因与改良措施如表1-21所示。
表1-21 与设计有关的原因与改良措施

1.3.10 烧焦纹
1.表观
塑件表面表现出银色和淡棕色的非常暗的条纹。
2.物理原因
烧焦暗纹是熔料过度热降解造成的。淡棕色的暗纹是熔料发生氧化或分解造成的。银色条纹的形成一般是因为螺杆、止逆环、喷嘴、浇口、塑件内窄的横截面或锐边区域产生了摩擦。
一般来说,在机器停工而料筒仍继续加热的时间内塑料会发生严重降解或分解现象。
如果仅在浇口附近发现条纹,原因就不只是热流道温度控制优化不足,还与注塑机的喷嘴有关。
熔料的温度哪怕是稍微有点高,熔料在料筒内的残留时间相对较长,也会导致塑件的力学性能下降。在因为分子热运动而产生的降解连锁反应的作用下,熔料的流动性会增加,使模件不可避免地产生溢模的现象。对于复杂模具尤其要小心。
3.加工原因
与加工参数有关的原因与改良措施如表1-22所示。
表1-22 与加工参数有关的原因与改良措施

4.设计原因
与设计有关的原因与改良措施如表1-23所示。
表1-23 与设计有关的原因与改良措施

1.3.11 玻璃纤维银纹
1.表现
加入了玻璃增强纤维的塑件表面呈多样缺陷,如灰暗、粗糙、部分出现金属亮点等,尤其是在凸起部分料流区,流体再次会合的接合线附近。
2.物理原因
如果注射温度太低并且模温太低,含有玻璃纤维的材料往往在模具表面凝结过快,此后玻璃纤维再也不会嵌入熔体内。当两股料流的前锋相遇时,玻璃纤维的取向是在每条细流的方向上,因此在料流交叉的地方会导致表面材质不规则,形成熔接痕或料流线。
这些现象在料筒内熔料未完全混合时会更加明显。例如,由于螺杆行程太长,导致混合不均的熔料被注入熔体口。
3.加工原因
与加工参数有关的原因与改良措施如表1-24所示。
表1-24 与加工参数有关的原因与改良措施

1.3.12 顶白
1.表现
在塑件面对喷嘴一侧,即在顶出杆位于模具顶出一侧的地方发现应力泛白和应力升高的现象。
2.物理原因
如果所需的脱模力太高或顶出杆的表面相对较小,此处的面压力会很高,发生变形、最终造成顶出部位泛白。
3.加工原因
与加工参数有关的原因与改良措施如表1-25所示。
表1-25 与加工参数有关的原因与改良措施

4.设计原因
与设计有关的原因与改良措施如表1-26所示。
表1-26 与设计有关的原因与改良措施
